高電圧コネクタの概要
高電圧コネクタ(高電圧コネクタとも呼ばれる)は、自動車用コネクタの一種です。一般的には動作電圧が60Vを超えるコネクタを指し、主に大電流の伝送を担います。
高電圧コネクタは、主に電気自動車の高電圧・高電流回路で使用されます。電線と連携して、バッテリーパックのエネルギーを様々な電気回路を通して、バッテリーパック、モーターコントローラー、DCDCコンバーターなどの車両システム内の様々なコンポーネントに伝送します。コンバーターや充電器などの高電圧コンポーネントにも使用されます。
現在、高電圧コネクタには主に3つの規格体系があり、LV規格プラグイン、USCAR規格プラグイン、日本規格プラグインの3つがあります。これらの3つの規格の中で、LV規格は国内市場における流通量が最も多く、プロセス規格も最も充実しています。
高電圧コネクタ組立工程図
高電圧コネクタの基本構造
高電圧コネクタは、主に接触器、絶縁体、プラスチック シェル、アクセサリの 4 つの基本構造で構成されます。
(1)接点:電気的接続を完成させる中心となる部品、すなわち、オス端子、メス端子、リードなど。
(2)絶縁体:接点を支持し、接点間の絶縁を確保するもの、すなわち内部のプラスチックシェル。
(3)プラスチックシェル:コネクタのシェルは、コネクタの位置合わせを確保し、コネクタ全体、つまり外側のプラスチックシェルを保護します。
(4)付属品:構造付属品および取り付け付属品を含み、具体的には、位置決めピン、ガイドピン、接続リング、シールリング、回転レバー、ロック構造など。
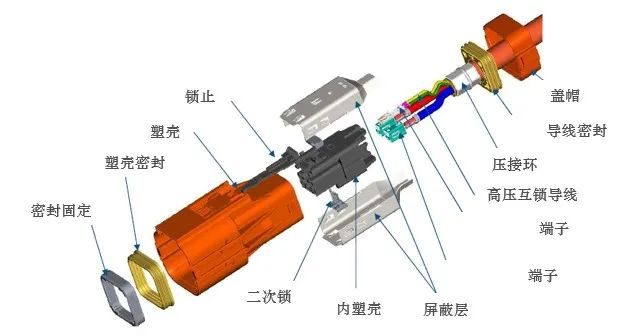
高電圧コネクタの分解図
高電圧コネクタの分類
高電圧コネクタは様々な方法で区別できます。コネクタにシールド機能があるかどうか、コネクタのピン数などによってコネクタの分類が定義されます。
1.シールドの有無
高電圧コネクタは、シールド機能の有無によって、非シールドコネクタとシールドコネクタに分けられます。
シールドなしコネクタは、比較的シンプルな構造でシールド機能がなく、比較的低コストです。充電回路、バッテリーパック内部、制御内部など、金属ケースで覆われた電気機器など、シールドを必要としない箇所に使用されます。
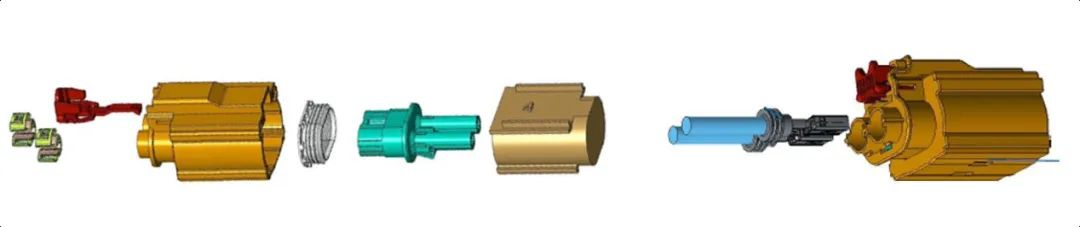
シールド層と高電圧インターロック設計のないコネクタの例
シールドコネクタは構造が複雑で、シールド要件が厳しく、比較的コストが高いという欠点があります。電気機器の外部と高電圧配線ハーネスを接続する箇所など、シールド機能が求められる箇所に適しています。
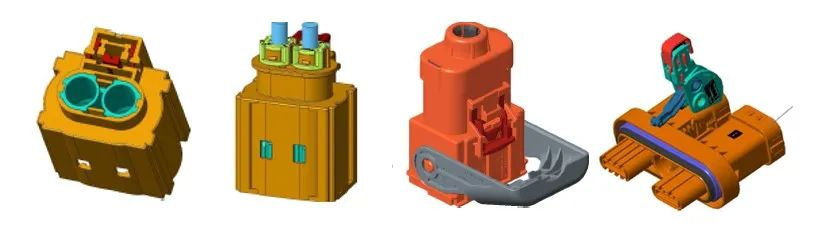
シールド付きコネクタとHVIL設計の例
2. プラグの数
高電圧コネクタは、接続ポート(PIN)の数によって分類されます。現在、最も一般的に使用されているのは、1Pコネクタ、2Pコネクタ、3Pコネクタです。
1Pコネクタは構造が比較的シンプルでコストが低いため、高電圧システムのシールドおよび防水要件を満たしていますが、組み立て工程がやや複雑で、リワーク作業性が悪いという欠点があります。一般的にはバッテリーパックやモーターに使用されます。
2Pおよび3Pコネクタは構造が複雑で、比較的コストが高い傾向があります。高電圧システムのシールドおよび防水要件を満たし、メンテナンス性に優れています。一般的には、高電圧バッテリーパック、コントローラ端子、充電器のDC出力端子などのDC入出力に使用されます。
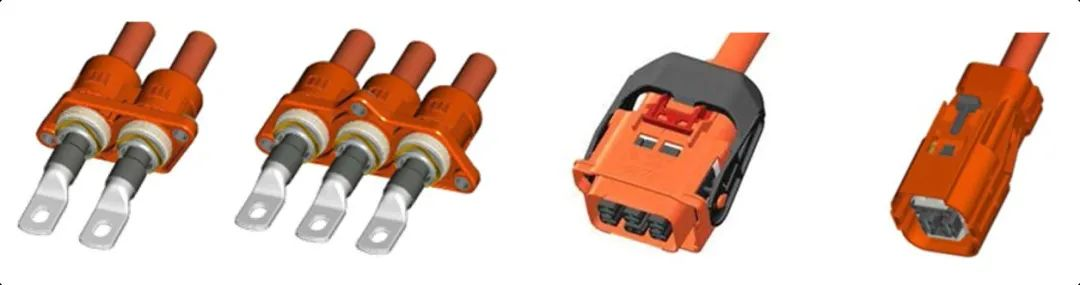
1P/2P/3P高電圧コネクタの例
高電圧コネクタの一般的な要件
高電圧コネクタは、SAE J1742 で規定された要件に準拠する必要があり、次の技術要件を満たす必要があります。
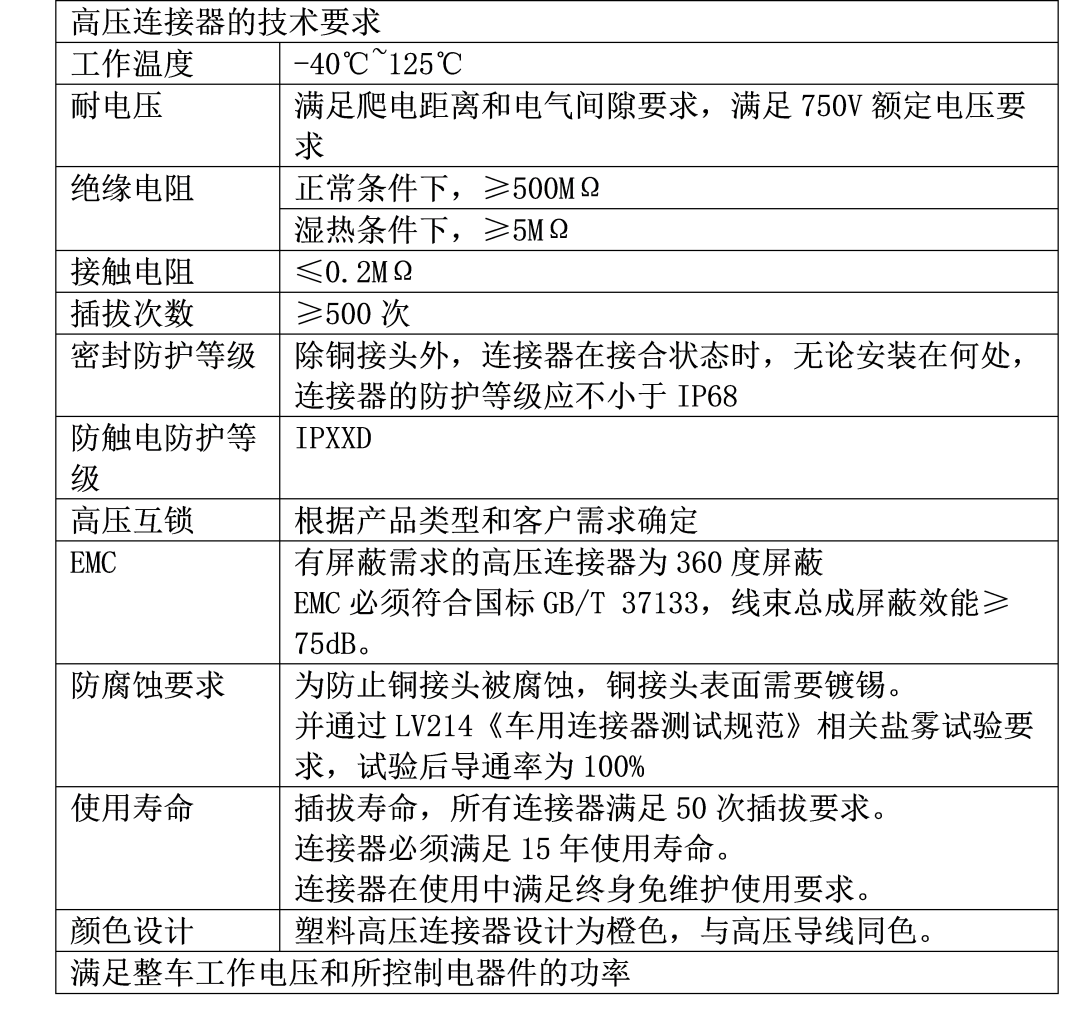
SAE J1742で規定された技術要件
高電圧コネクタの設計要素
高電圧システムにおける高電圧コネクタの要件には、高電圧および高電流性能、さまざまな動作条件(高温、振動、衝突衝撃、防塵および防水など)でより高いレベルの保護を実現できること、設置性があること、優れた電磁シールド性能があること、コストをできるだけ低く抑えて耐久性があることなどが含まれますが、これに限定されません。
高電圧コネクタが備えるべき上記の特性と要件に応じて、高電圧コネクタの設計の開始時に、次の設計要素を考慮し、対象を絞った設計とテスト検証を実行する必要があります。
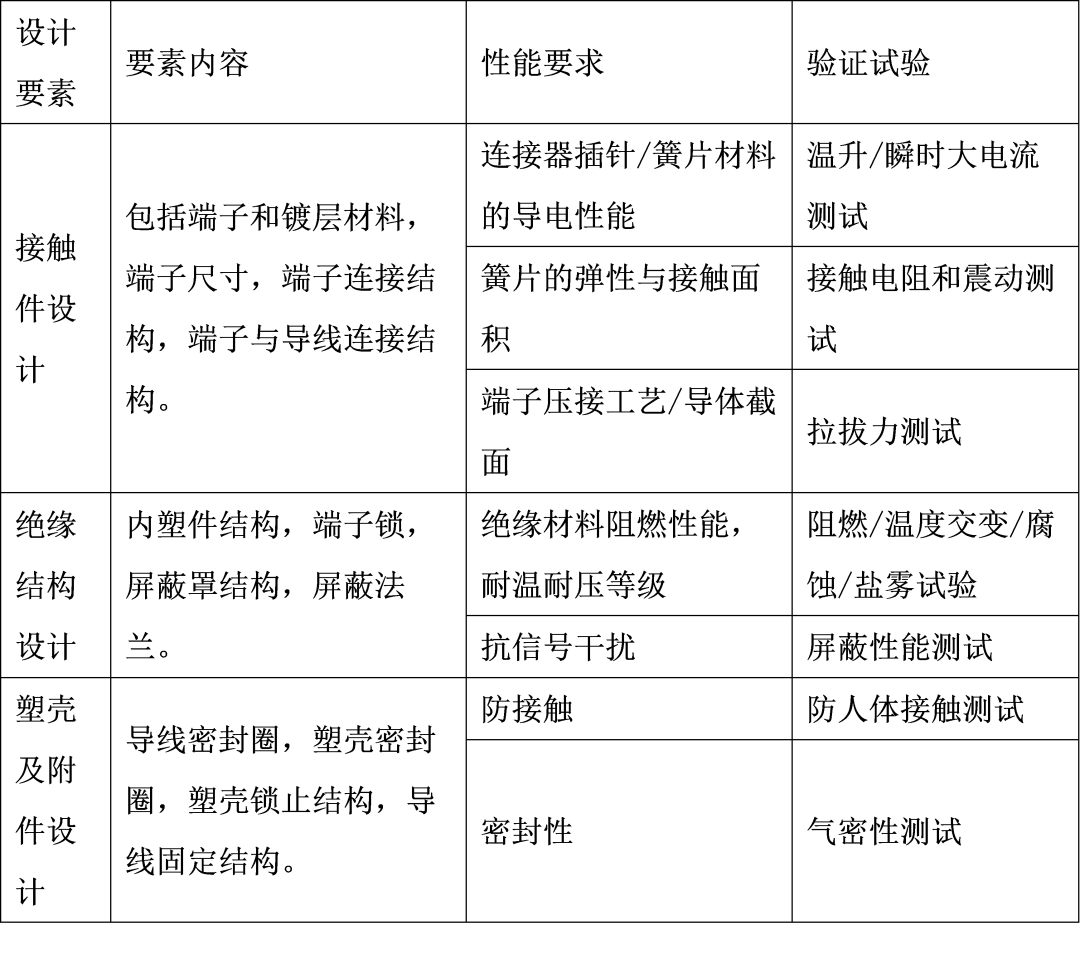
高電圧コネクタの設計要素、対応する性能、検証テストの比較リスト
高電圧コネクタの故障解析と対策
コネクタ設計の信頼性を向上させるには、まずその故障モードを分析し、それに応じた予防設計作業を行う必要があります。
コネクタには通常、接触不良、絶縁不良、固定不良という 3 つの主な故障モードがあります。
(1)接触不良については、静的接触抵抗、動的接触抵抗、単孔分離力、接続ポイント、部品の耐振動性などの指標で判断できる。
(2)絶縁不良については、絶縁体の絶縁抵抗、絶縁体の時間劣化率、絶縁体、接点およびその他の部品のサイズ指標を検出して判断することができます。
(3)固定式および分離式の信頼性については、端子およびコネクタの組み立て公差、耐久モーメント、接続ピンの保持力、接続ピンの挿入力、環境ストレス条件下での保持力などの指標を試験して判断することができる。
コネクタの主な故障モードと故障形態を分析した後、コネクタ設計の信頼性を向上させるために次の対策を講じることができます。
(1)適切なコネクタを選択します。
コネクタの選択は、接続する回路の種類と数だけでなく、機器の構成を容易にする要素も考慮する必要があります。例えば、丸型コネクタは長方形コネクタよりも気候や機械的要因の影響を受けにくく、機械的摩耗も少なく、電線端末への接続も確実であるため、可能な限り丸型コネクタを選択する必要があります。
(2)コネクタのコンタクト数が多いほど、システムの信頼性は低下します。したがって、スペースと重量に余裕がある場合は、コンタクト数の少ないコネクタを選択するようにしてください。
(3)コネクタを選定する場合には、機器の動作条件を考慮する必要があります。
これは、コネクタの総負荷電流と最大動作電流が、周囲環境の最高温度条件下での動作時に許容される熱に基づいて決定されることが多いためです。コネクタの動作温度を下げるには、コネクタの放熱条件を十分に考慮する必要があります。例えば、コネクタの中心から離れた接点に電源を接続することで、放熱性を高めることができます。
(4)防水性、耐腐食性がある。
コネクタが腐食性ガスや液体のある環境で動作する場合、腐食を防止するため、設置時に側面から水平方向に取り付ける可能性に注意してください。垂直方向に取り付ける必要がある場合は、液体がリード線に沿ってコネクタ内に流入するのを防ぐ必要があります。一般的には防水コネクタを使用してください。
高電圧コネクタ接点の設計における重要なポイント
接触接続技術は、端子と電線との接触接続、端子同士の接触接続など、主に接触面積と接触力を調べます。
接点の信頼性は、システムの信頼性を決定する重要な要素であり、高電圧配線ハーネスアセンブリ全体の重要な部分でもあります。一部の端子、電線、コネクタは過酷な使用環境により、端子と電線、端子と端子の接続部に腐食、老化、振動による緩みなどのさまざまな故障が発生しやすくなります。
損傷、緩み、脱落、接触不良などにより発生する電線ハーネスの故障は、電気システム全体の故障の50%以上を占めるため、車両の高電圧電気システムの信頼性設計においては、接触部の信頼性設計に十分な注意を払う必要があります。
1. 端子と電線間の接触接続
端子と電線の接続とは、圧着工法または超音波溶接工法による接続を指します。現在、高圧ワイヤーハーネスでは圧着工法と超音波溶接工法が一般的に採用されていますが、それぞれ長所と短所があります。
(1)圧着工程
圧着工程の原理は、外力を用いて導体線を端子の圧着部に物理的に押し込むことです。端子圧着の高さ、幅、断面状態、引張力は、端子圧着品質の中核を成す要素であり、圧着品質を決定します。
しかし、微細加工された固体表面の微細構造は必ず粗く、凹凸があることに注意する必要があります。端子と電線を圧着した後、接触面全体が接触するのではなく、接触面上に散在するいくつかの点が接触します。そのため、実際の接触面積は理論上の接触面積よりも小さくなるはずであり、これも圧着工程の接触抵抗が高くなる理由です。
機械圧着は、圧力、圧着高さなどの圧着工程に大きく影響されます。生産管理は、圧着高さやプロファイル分析/金属組織分析などの手段を通じて実施する必要があります。そのため、圧着工程における圧着の均一性は平均的であり、工具摩耗の影響は大きく、信頼性は平均的です。
機械圧着による圧着工程は成熟しており、幅広い実用用途があります。これは伝統的な工程であり、ほぼすべての大手サプライヤーがこの工程を用いたワイヤーハーネス製品を製造しています。
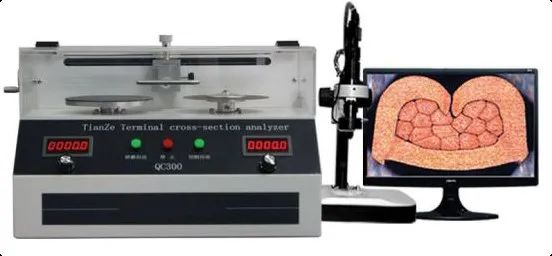
圧着プロセスを使用した端子およびワイヤ接点プロファイル
(2)超音波溶接プロセス
超音波溶接は、高周波の振動波を溶接する2つの物体の表面に伝播させます。圧力がかかった状態で、2つの物体の表面が互いに擦れ合い、分子層間の融合が起こります。
超音波溶接では、超音波発生器を用いて50/60Hzの電流を15、20、30、または40KHzの電気エネルギーに変換します。変換された高周波電気エネルギーは、トランスデューサーを介して再び同じ周波数の機械運動に変換され、その後、振幅を変化させることができるホーン装置を介して溶接ヘッドに伝達されます。溶接ヘッドは受信した振動エネルギーを溶接対象物の接合部に伝達します。接合部では、振動エネルギーが摩擦によって熱エネルギーに変換され、金属が溶融します。
性能面では、超音波溶接プロセスは、長時間接触抵抗が小さく、過電流による発熱が低いという特徴があります。安全性の面では、信頼性が高く、長時間の振動でも緩んだり外れたりしにくいという特徴があります。異なる材料間の溶接にも使用できます。表面の酸化やコーティングの影響を受けにくいという特徴があります。圧着プロセスの関連波形を監視することで、溶接品質を判断できます。
超音波溶接プロセスの設備コストは比較的高く、溶接する金属部品は厚すぎることはできません(通常、≤5mm)が、超音波溶接は機械的なプロセスであり、溶接プロセス全体を通して電流が流れないため、熱伝導と抵抗の問題はありません。高電圧ワイヤーハーネス溶接の将来の傾向です。
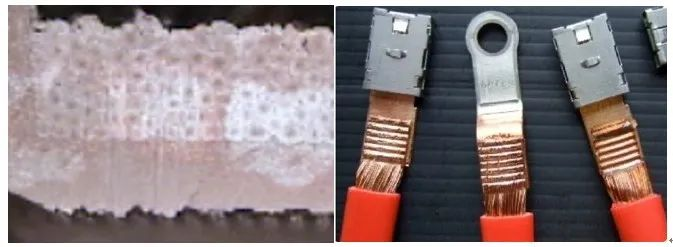
超音波溶接された端子と導体およびその接触断面
圧着工程または超音波溶接工程にかかわらず、端子を電線に接続した後、その引張力は規格要件を満たす必要があります。また、電線をコネクタに接続した後、引張力は最小引張力を下回ってはなりません。
投稿日時: 2023年12月6日